在科技飞速发展的时代背景下,制造业正经历着前所未有的智能化与自动化转型浪潮。作为新能源产业的基石,锂电池产业更是站在了这一变革的前沿。随着市场对锂电池性能要求的日益提升,生产线的智能化与自动化程度成为了衡量企业竞争力的关键指标。锂电池生产流程的每一个细节都直接关系到产品的安全性、耐用性以及整体性能,因此,实现生产过程中的精准控制与高效检测显得尤为重要。
视觉检测系统凭借其卓越的高精度与高效率特性,在锂电池生产线中占据了不可或缺的地位,被誉为生产线上的“智能眼睛”。该系统能够模拟人类视觉功能,通过高精度摄像头与先进图像处理技术,对锂电池的外观缺陷、尺寸精度、装配质量等进行非接触式、实时在线检测,确保每一环节都达到严格的质量标准。这种智能化检测手段不仅大幅提升了检测效率与准确性,还有效降低了人工检测带来的误差与成本,是推动锂电池产业向高质量、高效率发展的重要力量。
图1:视觉检测系统在锂电池生产线涂布工序中检测材料表面瑕疵、尺寸与对齐度,确保产品的一致性
视觉检测系统是一种基于计算机视觉技术的自动化检测系统,它通过摄像头等图像采集设备获取产品图像,利用图像处理算法对图像进行分析和处理,从而实现对产品外观、尺寸、位置等信息的检测。视觉检测系统具有高精度、高效率、非接触式检测等优点,已广泛应用于锂电池生产制造90%以上工序中。
视觉检测系统能够精确检测电池极片表面的各种缺陷,如划痕、凹陷、漏涂、斑点等。这些缺陷如果未能及时发现并处理,将直接影响电池的电化学性能和整体性能。通过高分辨率摄像头捕捉极片表面的图像,并结合先进的图像处理算法,系统能够自动识别并分类这些缺陷,确保只有符合质量标准的极片进入下一生产环节。这种非接触式的检测方式不仅提高了检测的准确性。
其次,视觉检测系统在电池极片的尺寸测量和形状检测方面也表现出色。极片的尺寸和形状精度对于电池的装配和性能有着直接影响。通过图像处理算法,系统能够自动提取极片、电芯的轮廓信息,并计算出精确的尺寸数据,为生产过程中的质量控制提供有力支持。
图2:极片表面瑕疵图例
视觉检测系统运用深度学习技术检测锂电池瑕疵,其原理在于通过海量缺陷图像数据训练AI模型,提取并分析锂电池表面的缺陷特征,实现高效、准确的瑕疵自动识别和精确分类,这一技术极大提升了瑕疵检测的效率和准确性,它大幅提升了瑕疵检测的效率和精度,确保了产品质量的稳定性和可靠性;不断优化生产工艺和设备性能也是提高产品质量和减少瑕疵的重要手段。同时,促进了锂电池生产向智能化、自动化转型,推动了新能源产业的快速发展。
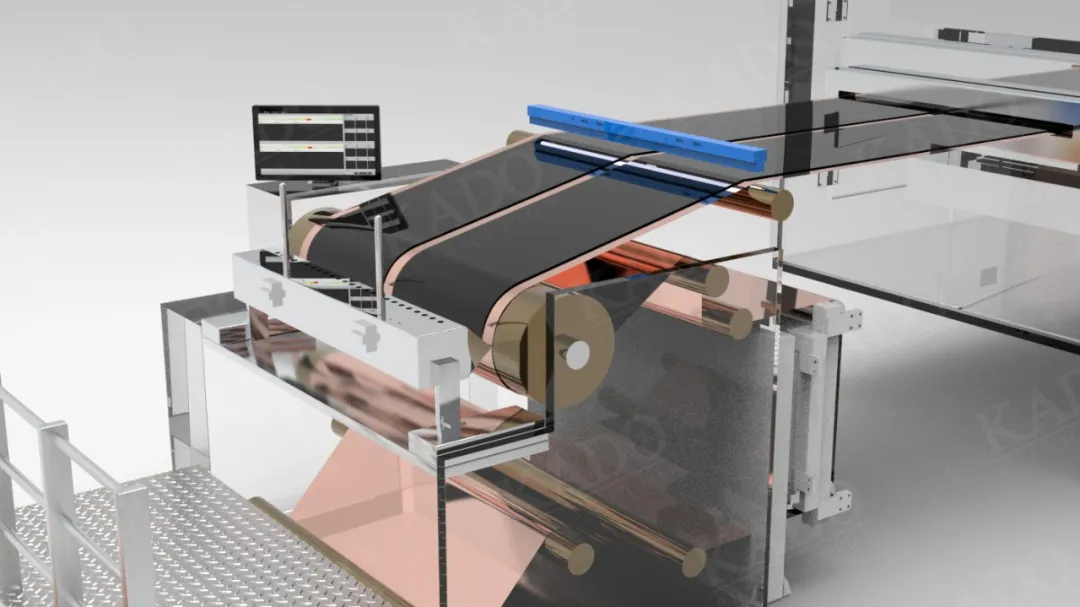
图3:视觉检测系统应用于锂电池生产过程的涂布工序(一次涂布)
图4:视觉检测系统应用于锂电池生产过程的涂布工序(二次涂布)
涂布线是锂电池生产中的前段核心工序之一,其主要任务是将稳定性好、粘度适宜的浆料均匀涂覆在金属箔表面,形成正负极极片。这一过程中,涂布精度直接影响电池的性能和安全性。通过高分辨率图像传感器(CCD、CLS)捕捉涂布后的极片表面图像,系统能够对涂层的尺寸和表面缺陷,如划痕、颗粒、气泡、涂层对齐度进行精确测量。这种非接触式的检测方式不仅提高了检测效率,还可搭配纠偏系统、不良标识系统实现生产的闭环控制需求。确保每一批次产品的质量稳定可靠。
图5:视觉检测系统应用于电池极片分切工序
对极片A/B面100%缺陷检测
分切后极片宽度检测+分切宽度闭环控制
分切机是锂电池生产中的关键设备之一,其主要功能是将极片分切成特定宽度,以便后续工序的加工和组装。然而,传统的分切机在分切过程中往往难以避免毛刺、波浪边和掉粉等缺陷的产生,这些缺陷对电池的性能和安全性构成严重威胁。
视觉检测系统在分切机上的应用,有效解决了这些问题。通过在分切机的入料和出料配置视觉检测系统,实时监测分切工序的极片质量。通过图像处理算法,系统能够自动识别并分类极片上的毛刺、波浪边和掉粉等缺陷,配合贴标机精准标记不良品,在后工序便于瑕疵产品的快速识别与隔离。让极片表面质量100%数据化对后工序的生产效率及一次良率起到至关重要的作用。
图6:电池卷绕工序用于对极片表面缺陷+贴胶后尺寸+隔膜表面缺陷+卷绕后卷芯外观尺寸检测等;
卷绕机是锂电池生产中的中段核心设备之一,其主要任务是将正负极片、隔膜等物料轮流叠放并卷绕成圆柱电芯或方型电芯。在卷绕过程中,极耳褶皱、极片错位等缺陷的产生会严重影响电芯的性能和安全性。视觉检测系统能够精准地识别极片和PE膜涂层上的各种缺陷,如划痕、裂纹、污点、异物、针孔、尺寸偏差等。这些缺陷如果未能及时发现,会导致锂电池的性能下降、寿命缩短甚至安全问题。通过视觉检测系统的实时监控与卷绕设备通讯联动控制,可以对有缺陷的极片或者隔膜进行单卷后不良排出,从而降低原料浪费,提高整体产品良率并有效提高设备稼动率。
视觉检测系统作为锂电池行业的智能眼睛,其高精度、高效率及非接触式检测特性,正深刻推动产业升级。它不仅大幅提升了产品质检的准确性与速度,减少了人工误差与成本,还通过非接触方式有效保护了产品表面,延长了设备使用寿命。更重要的是,视觉检测系统的可追溯性确保了生产过程的透明化与质量控制的闭环管理,为锂电池的安全性能提供了坚实保障。随着AI、大数据等技术的深度融合,智能视觉检测系统在自动化、智能化方面持续进化,能自主学习、优化检测算法,适应更复杂多变的生产环境,进一步提升检测效率与精准度。这一技术革新不仅促进了锂电池行业的快速发展,还带动了上下游产业链的技术升级与协同创新,为新能源汽车、储能等领域的蓬勃发展注入了强劲动力。